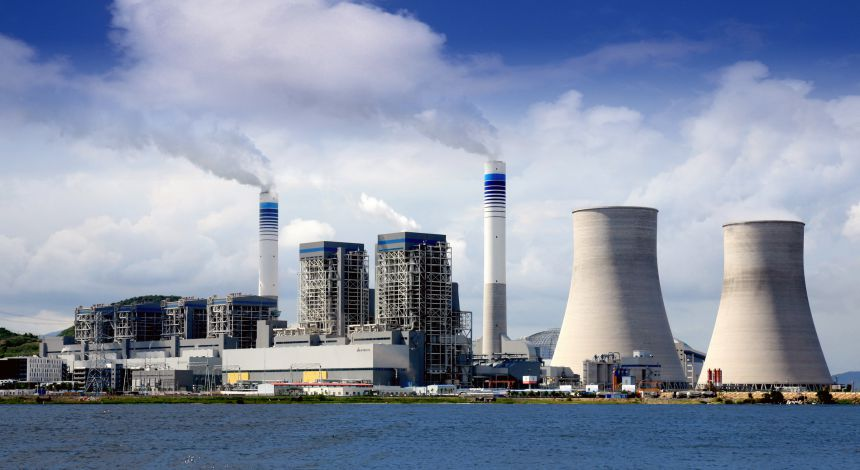
RO Model: LG BW 400 AFR
Active Area: 400 ft² (37 m²) | Permeate Flow Rate: 39.7 m³/d (10,500 GPD) | Stabilized Salt Rejection: 99.6%
Background
Cooling towers play a critical role in industries where large amounts of heat are generated by machinery or processes, such as in thermal power plants. As water scarcity continues to rise, power generation facilities face increasing operational challenges. For example, a typical thermal power plant generating around 1 billion kWh of energy annually uses approximately 24 million cubic meters of water, which is enough to meet the daily water needs of approximately 160 million people. An overwhelming 99% of this water is used as cooling tower make-up water for the plant’s cooling systems.
Project Introduction | |
Start-Up Date | May, 2021 |
Feed Water Intake | Drainage of circulating cooling water system |
Application | Boiler feed water treatment system |
Design Recovery | 0.75 |
Project Capacity | 14,688 m³/d |
Feed Temperature Range | 5°–35°C |
Feed Pressure Range | 5–12 bar |
Challenges of Cooling Tower Blowdown Water
One major consequence of cooling tower make-up water is the vast amount of drainage wastewater, known as cooling tower blow down water, wasted during the cooling process. With increasing water shortages, treating this blow down water has become essential to maintaining operational efficiency and sustainability. However, cooling tower blow down water contains high salt concentrations that can lead to corrosion, scaling, and fouling. It may also contain chemicals used to prevent scaling, regulate pH, inhibit corrosion, and control biological contaminants, all to protect the cooling tower equipment. As a result, the cooling tower process requires large amounts of both freshwater and wastewater.
To overcome these challenges, many power plants have turned to reusing cooling tower blowdown water as an alternative water source. Reverse Osmosis (RO) has emerged as one of the most efficient technologies for producing high-quality permeate that aligns with reuse standards for cooling tower make-up water. However, RO membranes are susceptible to foulants from wastewater, which can quickly degrade performance and lead to further replacements.
LG NanoH2O™ RO Membranes Significantly Improve the Performance of Cooling Tower Blowdown Water Treatment
In 2021, LG Water Solutions supplied 540 units of its anti-fouling BW 400 AFR RO membranes to one of China’s leading power plants by CHN Energy Investment Group. This initiative effectively optimized water usage efficiency and achieved outstanding customer satisfaction. Since the treated source water was primarily cooling tower blowdown water, the key requirement was ensuring that the RO membranes maintained high performance despite severe fouling conditions and prolonged use. By providing its anti-fouling BW 400 AFR product, LG Water Solutions helped the end-user achieve these objectives.
The RO system, which began operation in May 2021, has been running efficiently for over three years. Based on operational data and customer feedback, the train installed with LG BW 400 AFR membranes has demonstrated a lifespan 1.5 to 2 times longer than that of the Product A train installed with Company A’s anti-fouling membranes (see figure 1).
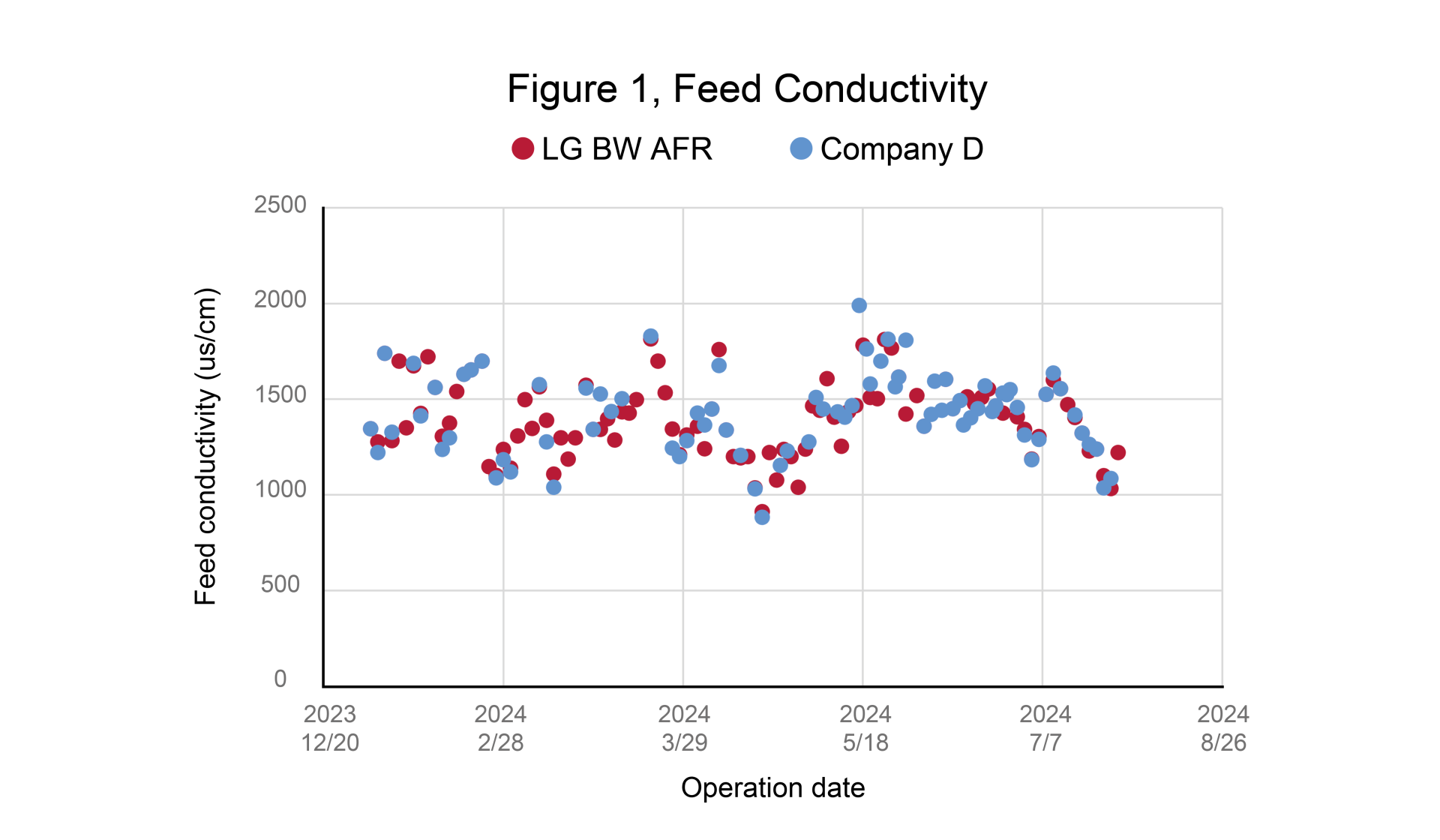
Under high fouling conditions, the LG train’s average permeate flow was 6.7% higher than that of Product A’s train. Furthermore, the recoveries of the LG and Product A’s trains are around 70.1% and 55.9%, respectively, indicating that the BW 400 AFR membranes can treat more water for reuse at the power plant (see figure 2).
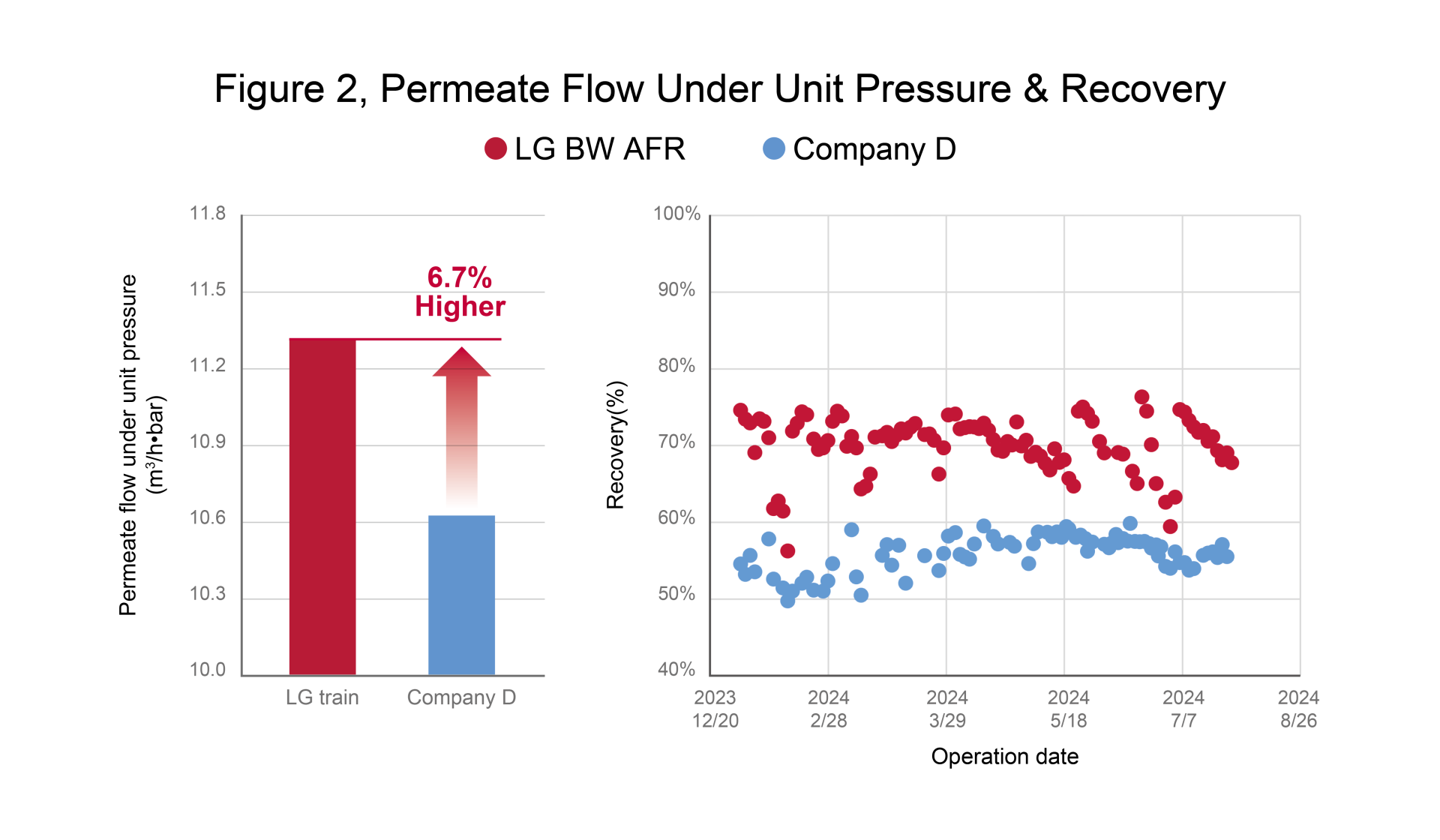
“Under high fouling conditions, normalized differential pressure (NDP) of the LG train was approximately 1 bar lower than that of Product A’s train, indicating significantly better fouling resistance of BW 400 AFR” (See figure 3)
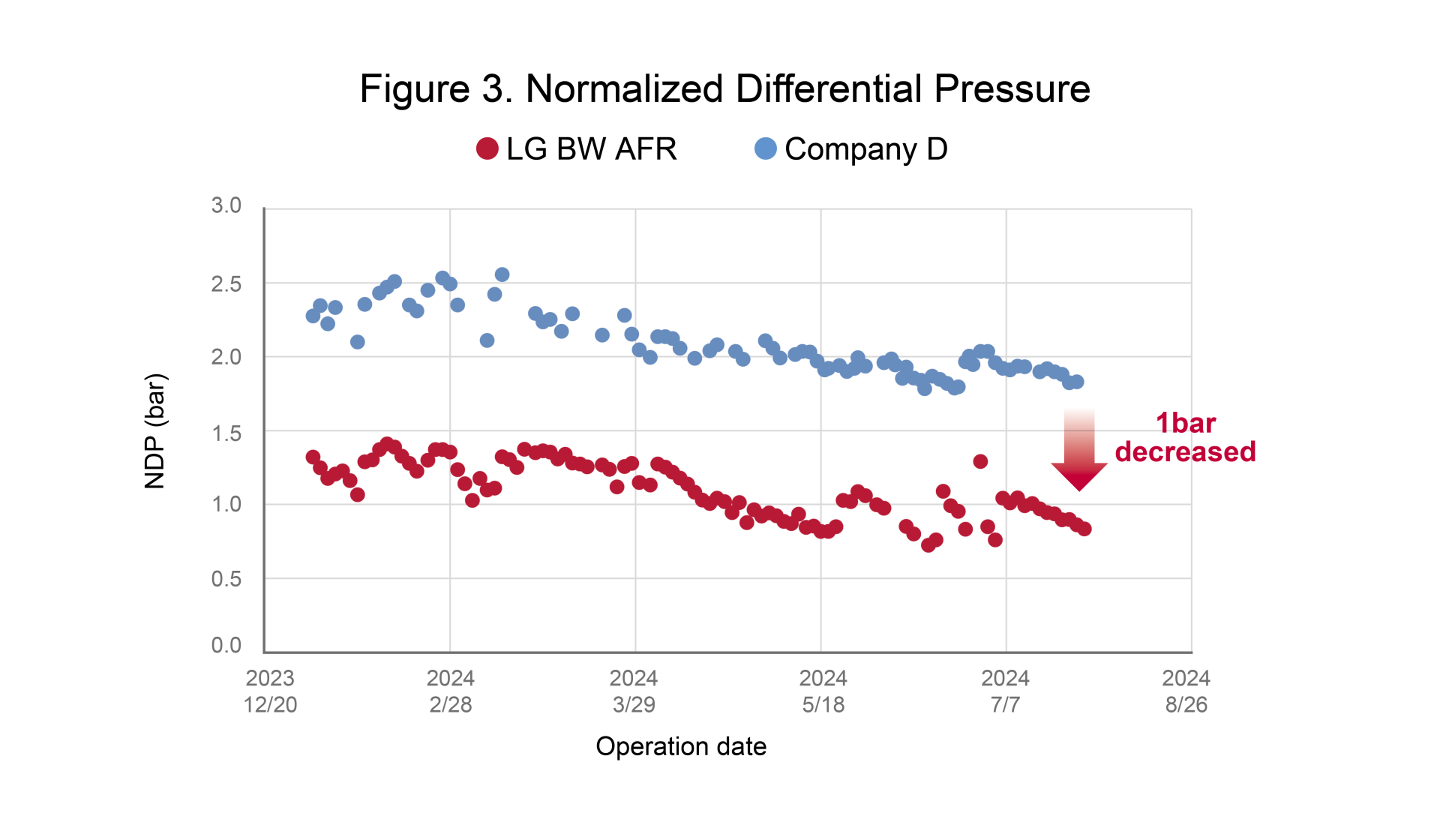
Result
After more than three (3) years of treating cooling tower blowdown water, the RO system with LG BW 400 AFR membranes has maintained high permeate flow, high recovery, low normalized differential pressure (average NDP of approximately 1.09 bar), and high normalized salt rejection (average salt rejection around 99.4%). These results highlight LG Water Solutions’ commitment to delivering reliable, high-performance systems that drive long-term operational efficiency.
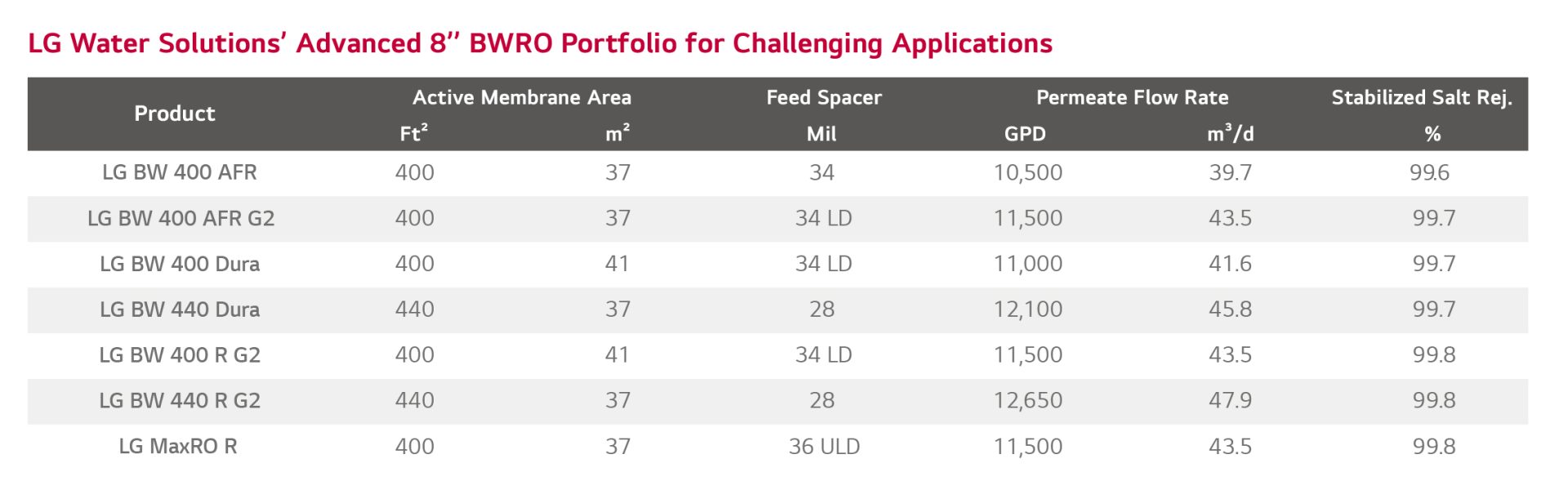